» AlfaSources
Chromate-free metal vapour sources for different applications in industry and research:
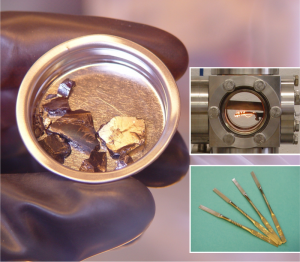
- Bose-Einstein-Condensation
- Magneto-Optical-Traps
- Photomultiplier Tubes
- Atom Clocks
- OLED
- fundamental research
This kind of metal vapour source was developed by Alvatec Alkali Vacuum and Technologies GesmbH, therefore the name Alvasource is also in use. Other names are dispenser, evaporator, source, oven.
» Table Of Content
» Alkali Alloy
» The Principle of AlfaSources
» Mounting
» Activation, Evaporation, Bake-out
» Sequence from evacuation to evaporation
» Table of Temperatures
» Current-Temperature-Graph
» Atomic Beam
» Minimum Durability and Storage
» Dimensions
» Alkali Alloy
The relatively low boiling point or sublimation point of alkali metals makes pure alkali metals inappropriate for use in high vacuum evaporators which are usually baked out at temperatures between 200°C and 400°C for many hours. This low boiling and sublimation temperature of pure alkali metals can however be significantly increased.
Alkali metals form many stable, high melting intermetallic compounds with non-toxic metals, like indium, gallium, tin or bismuth.
An example is the high formation enthalpy of bismuth-caesium compounds like
Bi2Cs (melting point 868K/595°C) or BiCs3 (MP 923K/650°C) – also see BiCs phase diagram. The sublimation temperature of the intermetallic compound Bi2Cs at a pressure of 1×10-4 Pa is about 723K/450°C, which is 430K more than the sublimation temperature of pure caesium which is 295K/22°C at a pressure of 1×10-4 Pa. Our standard alkali alloys are ideal for the application in high vacuum.
» The Principle of AlfaSources
The desired alloy containing the alkali metal is specially produced under ultra high vacuum conditions in our company. A small stainless steel tube – which is gas-tight sealed by a pressed indium sealing – is filled with the alloy or pure element under argon atmosphere.
When used, the source is heated via conventional resistance heating. Or heating the whole chamber. As a consequence, the indium sealing melts and the small argon puffer is pumped away during the standard bake-out procedure.
A mechanical unsealing of the indium seal is also possible. In this case it has to be considered that the mechanical treatment and the subsequent transport in your application has to be carried out under inert atmosphere.
The AlfaSource releases the desired ultra-pure alkali metal when the required sublimation temperature is reached due to the activation current. There is only one physical natural limit when using AlfaSources: the temperature, i.e. the current, must not be increased above the indicated specification limit to prevent sublimation of non-alkali metals in the alloy and to prevent the AlfaSource from melting like a fuse.
» Mounting
The design of the AlfaSources guarantees easy handling and functionality. The contact flabs can be attached with simple clamps in each vacuum chamber.
- Mounting
Type S can be installed both horizontally and vertically (slot opening on top). The opening can be directed downwards in the horizontal installation in order to allow evaporation downwards.
Types F and C are designed for horizontal installation. As long as the opening is pointing upwards, an aslope to vertical installation is also possible.
Type V is designed for horizontal installation.
» Activation » Bake-out » Evaporation
AlfaSources can be mounted under ambient air conditions. Avoid bending of the sources, otherwise the seals can get leaky. Also do not damage the rippled areas (with the zig-zag or X pattern) of the contact flaps: No drilling or trimming!
- Heating
can result from current flow or external heating.
The current flow varies due to the selected temperature, type and size of the AlfaSource and the installation situation and the electrical generator used. For this reason, the relationship between current and temperature given below is to be understood as orientation only. Depending on their specific installation situation, the values may differ considerably. The desired temperatures must be achieved by slowly increasing the current. When the current changes, it may take a few minutes until a stable temperature level is reached again.
When heating the vacuum chamber from outside, note the long reaction time between a change in temperature outside the chamber and the temperature at the AlfaSource – after all, there is a perfect vacuum insulation 😉
- Activation
Activation results from melting the indium seal while the vacuum pump is running and can be monitored by measuring the total pressure. The temperature at the seal should be 450K for 30 minutes. If the bake out temperature at least 600K the activation temperature my be raised to 500K and the time can be reduced to 10 minutes. 450K is usually reached with 1.2 and 4.0 A – depending on size, type and installation situation. Argon is released and generates one or more short pressure peaks.
- Bake-out
The Bake-out must stay within the specified temperature limits and can include activation at the same time. Please note: Some elements have a lower bake-out temperature than is required during activation.
- Evaporation
The element evaporates between 3 A and 17 A, depending on size, type and installation situation, respective corresponding to the temperature table. The rate of evaporation increases with higher temperature and decreases over time.
» Sequence from evacuation to evaporation
- pump down at room temperature until =< fine vacuum
- heat the vacuum chamber and the AlfaSource to ~100°C and continue pumping down.
- when the high vacuum range is reached, heat the AlfaSource to approx. 200-220°C to melt the indium seal = activation.
- check the activation by measuring the pressure: one or more pressure peaks can be measured, followed by a rapid drop in pressure. If the pressure remains rather constant, the (liquid) indium seal has closed again and heating must be prolonged and/or increased.
- Afterwards, the AlfaSource can be baked out to achieve UHV. Please note the maximum temperatures indicated, which are also pressure-dependent.
Attention:
- It is often necessary to use a sufficiently high temperature in order to keep the bake-out time low, however, the element in the AlfaSource must not be accidentally evaporated. In general, the recommendation is to stay 100K below the boiling temperature (temperature depending on the current pressure level).
- With non-activated AlfaSources, sudden increases in current can lead to serious damage.
» Table Of Temperatures
For the maximum allowable temperatures for bake-out, activation and evaporation check the table below. Bake-out = evaporation temperature – 100K (minimum, better -200K) The temperatures for bake-out and evaporation depend on the pressure. The currents corresponding to the temperatures are on the next point in the current-temperature graph. Activation temperature 450K for at least 20 minutes.
Beware of processes in which your ordered element evaporates below the melting temperature of indium. The AlfaSource is filled with the inert gas argon, so until activation (pressure peak) your element is almost under normal pressure. After activation and the pumping out of the argon, however, your element may start to evaporate unintentionally due to the low pressure and temperature during activation.
In such cases (written in italics in the table, with a tolerance of +100K), it is necessary to reduce the temperature after activation and before the critical pressure is reached even if the bake-out time is then extended.
Activation Tmax | Evaporation Tapprox. | |||||||
---|---|---|---|---|---|---|---|---|
pressure max Element/note | 1×10-2 Pa | 1×10-2 Pa | 1×10-4 Pa | 1×10-6 Pa | 1×10-8 Pa | |||
Al / pure | 450-470 K | n.pos. | ~1090 K | ∼958 K | ~861 K | |||
Ba / pure | 450-470 K | ~750 K | ~650K | ∼566 K | ~504 K | |||
Ca / pure | 450-470 K | ~720 K | ~630 K | ∼551 K | ~492 K | |||
Cd / pure | 450-470 K | ~450 K | ~390 K | ∼342 K | ~306 K | |||
Ce / pure | 450-470 K | n.pos. | n.pos. | n.pos. | ~1139 K | |||
Cs / (alloy) CsBi25 | 450-470 K | ∼590 K | ||||||
Cs / (alloy) CsSn50 | 450-470 K | ∼800 K | ||||||
Er / pure | 450-470 K | n.pos. | ~1080 K | ∼947 K | ~860 K | |||
Ho / pure | 450-470 K | n.pos. | ~1043 K | ∼918 K | ~821 K | |||
K / (alloy) KBi40 | 450-470 K | ∼610 K | ||||||
K / (alloy) KBi67 | 450-470 K | ∼730 K | ||||||
K / KCl + Ca | 450-470 K | ~780 K | ~600 K | ∼520 K | ||||
Li / pure | 450-470 K | ~670 K | ~580 K | ∼505 K | ~445 K | |||
Mg / pure | 450-470 K | ~600 K | ~520 K | ∼462 K | ~404 K | |||
Na / (alloy) NaBi25 | 450-470 K | ∼900 K | ||||||
O2 / BaO2 | 450-470 K | ∼900 K | ||||||
Pr / pure | 450-470 K | n.pos. | n.pos. | ∼1075 K | ~984 K | |||
Rb / (alloy) RbBi40 | 450-470 K | ~730 K | ∼650 K | |||||
Sb / pure | 450-470 K | ~700 K | ~610 K | ∼550 K | ||||
Sr / pure | 450-470 K | ~670 K | ~571 K | ∼504 K | ~450 K | |||
Yb / pure | 450-470 K | ~625 K | ~546 K | ∼486 K | ~440 K | |||
Tabelle 1, Source: Mainly Vapour Pressure Calculator of the TU Vienna |
» Current-Temperature-Graph
The temperature at the stainless steel tube can be determined by the dependence of the temperature of the applied current in the following graph. The values are different for each vacuum system, therefore these values are to be seen as guidelines. I strongly recommend slowly increasing the current – and thus the temperature of the source. It takes several minutes until a new equilibrium and thus a stable temperature has been established. With non-activated AlfaSources, sudden increases in current can lead to serious damage.
Please note that each temperature curve stands for several AlfaSource types:
- 2F = 2F & S, 2C, 2L, 2Z
- 3F = 3F & 3S, 3C, 3L, 3Z
- 5F = 5F & 5S, 5C, 5L ,5Z
- 7F = 7F & 7S, 5C, 5L, 5Z
» Atomic Beam
The escaping atomic beam is not bundled and radiates all around in 180 °. Exceptions are shadows caused by the contact flabs. The main direction is close to the axial direction of the cylindrical part of the source (or at right angles to it for type S). The particle density is almost normally distributed, so it decreases sharply towards the edge.
» Minimum durability and Storage
The minimum shelf life of the AlfaSources mainly depends on the type of storage at the customer!
- Minimum durability of the AlfaSource: 3 months after date of production
- Minimum durability if the jar is unopened : 12 months after date of production
- Minimum durability if the unopened jar is under Argon 5.0: > 3 years
- Alkali alloys and KCl : shelf life +50%
- ATTENTTION: Do not store under vacuum!